WhatsApp:+86-19061507566 Email:Jason@hdazfastener.com
The difference between non-standard screws and standard screws
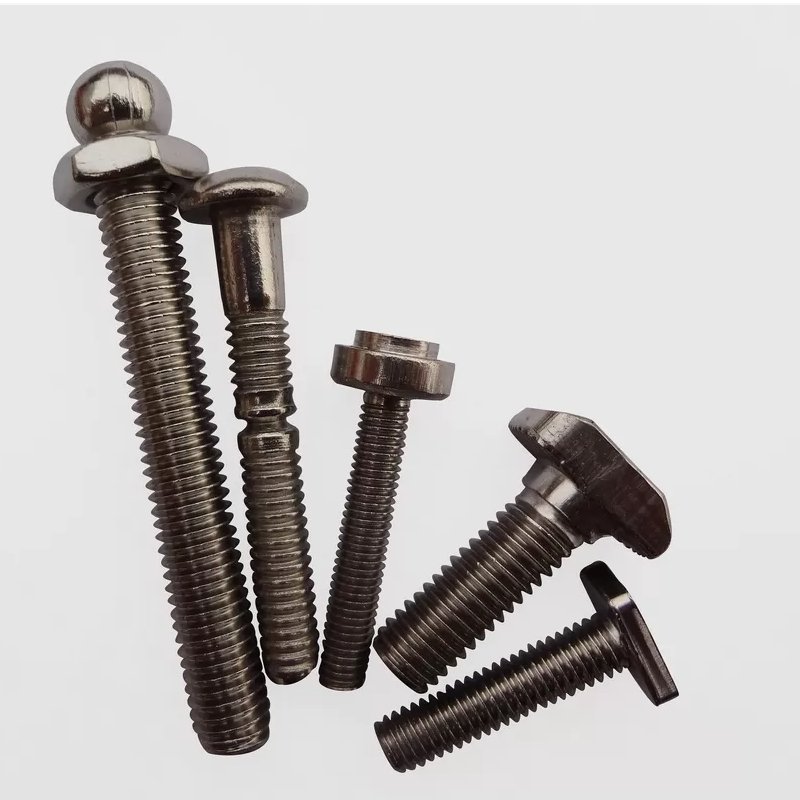
With the advancement of science and technology, the development of non-standard screw customization has also made a high-quality leap. There is a certain foothold in the field of non-standard threads, from the design of non-standard threads to the research and development and production of mold opening. Non-standard screw factories have their own perfect production management systems such as design, research and development, customization, production, and after-sales service. Let’s take a look at the difference between non-standard screws and standard screws!
Compared with standard screw fasteners, non-standard screws show excellent characteristics in many aspects. In the face of huge market demand, we need to keep up with the development of the times and keep up with the development of society. This is also the reason why screw manufacturers decided to take the road of non-standard screw customization. The screws have almost no inventory and no spot. Non-standard screws are only suitable for a certain enterprise or product, so they have uniqueness and unique properties. When producing, the production technology is also different from that of standard threads.
For example, moisture-proof, moisture-proof and moisture-proof methods for non-standard screws
- Use solvent-free spraying for non-standard screws used in vibration machinery as much as possible;
- It is preferred to choose epoxy-urethane (Epoxy-urethane) system or unmodified epoxy) system and other impregnation coatings that do not contain oxidizing components;
- When using melamine acid impregnation coatings, the non-standard thread, curing temperature and curing time should be adjusted. The curing temperature should be slightly higher than 130 (such as 135), and the curing time should be greater than 180min. The process must be strictly followed. Especially in hot and humid seasons, the drying (curing) time of the paint specified in the paint factory sample may not be sufficient from the perspective of rust prevention, and the motor has specific internal
- Use paint that does not contain volatile acids;
- Choose paint with good hydrolysis resistance.
Tips for controlling the quality of non-standard screw coating
The quality inspection of non-standard screws is generally considered from the appearance and the quality effect of the coating, among which the quality and corrosion resistance of non-standard screws are measured, and the appearance of non-standard screws. The corrosion resistance is tested after setting the test conditions. The electroplating quality of non-standard screws is controlled from the following two aspects.
- From the appearance of electroplated screws, the product surface shall not have local non-plating, scorching, roughness, dimness, peeling, crusting and obvious stripes, and shall not have pinholes, black electroplating slag, loose passivation film, cracking, shedding and severe passivation marks
- The plating thickness of electroplated screws, the plating surface must be smooth and the thickness must be uniform. The working life of fasteners in corrosive atmospheres is proportional to the thickness of their plating. The general economic plating is 4~12um, the standard average thickness of hot-dip galvanized screws is 54um, and the minimum thickness is 43um. The above data is for reference only.
The above is the difference between non-standard screws and standard screws. If you need to know more, please feel free to contact us!